The Most Overlooked Truck Repairs That Cost You Later
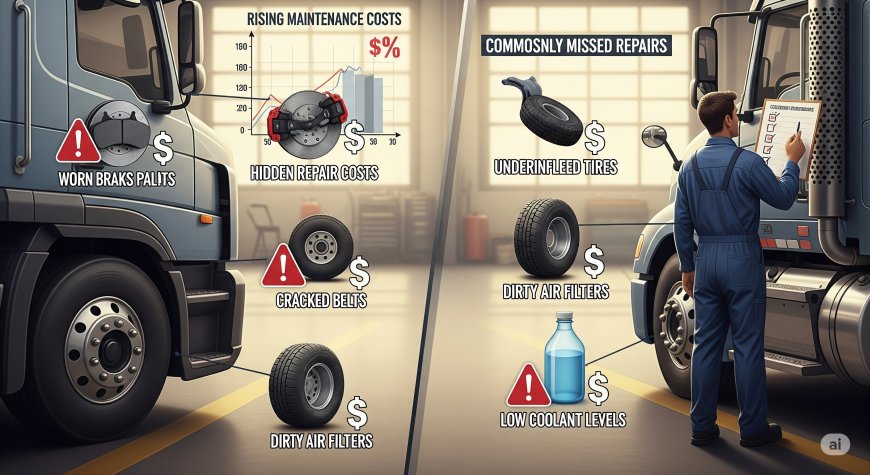
You have a bus to plan, workers to hire, regulations to stay on top of, and that after-hours phone call to the busybody, so what seems like a minor mechanical problem gets swept away on the back burner. However, there is a twist to it; a small oversight may result in a complete breakdown and the loss of loads, and a huge impact on your pocket. To the dismay of many fleet owners and owners, putting off repair on trucks more often than not pays way beyond the repair.
Have you ever thought, 'Oh, that can wait until next week or so,' then you are not the only person thinking that way. But, speaking of the most underestimated repairs that kick back, what about truck repairs?
1. Brake Wear and Slack Adjusters Are the Silent Load Killers
Brakes are easy to take for granted, especially if your truck is still stopping smoothly. But once a brake shoe starts thinning or a slack adjuster slips out of spec, it’s only a matter of time before you’re flagged during a DOT stop or worse, end up with a runaway load on a downhill grade.
The irony? These components give signs. A slight pull during braking, a faint grinding, or longer stopping distances. But a lot of drivers simply change their mode of driving and forget. Stalk-free and out of emergency repair bays: regular repairs of the trucks, including a routine check of the brakes.
2. Leaky Wheel Seals: Small Drip, Big Drama
Wheel seals seem like a minor nuisance until the oil leak ruins your brakes or leads to bearing failure on the highway. These leaks are often hard to catch unless someone’s checking tires and hubs consistently.
If you’ve got a mechanic wiping down wheel hubs during PMs, that’s great. But if your team skips this step or doesn’t even do PMs on schedule, that small drip could cost you a roadside tow, brake contamination, and a pricey axle rebuild.
3. Faulty Lights Are DOT Magnets
A single broken marker light may not seem like a big deal until it triggers a full roadside inspection. Lights are among the top reasons trucks get pulled over, and once you’re stopped, inspectors don’t just check bulbs. They dig deeper.
Many truck repairs start with a simple lighting issue that spirals into CSA points, delayed deliveries, and surprise citations. Swapping bulbs and checking connectors during pre-trips takes minutes, but ignoring this detail could set off a costly chain reaction.
4. Air System Leaks Are the Invisible Problem
Air pressure issues don’t always scream for attention. A minor leak in your air line or fittings might just show up as a compressor running more often. Most drivers get used to the hiss or longer build-up time and move on.
But every air leak strains the system and increases wear on your compressor. Eventually, this leads to full system failure or inability to release the brakes. And when you’re stuck at the dock, unable to move, nobody’s happy, least of all your customer.
5. U-Joints and Drive Shaft Issues Cause the Underbody Danger
Out of sight, out of mind until a bad U-joint seizes or the drive shaft gives out on the highway. These aren’t just expensive truck repairs; they can be downright dangerous.
When your drivers start hearing clunks when changing gears, or clanking against the gear, or feeling some strange vibration, that is your alarm call. There should not be delays. Greasing and inspecting U-joints is not all that exciting, but it is better than sitting by the side of the road waiting three hours for the service to come.
6. Worn Belts and Hoses Are Ticking Time Bombs
Belts and hoses are the classic “we’ll do it next service” components. That is, until one snaps in the middle of a route and overheats the engine. These failures almost always happen at the worst possible time on a hot day, in the middle of nowhere, with a full reefer load ticking down.
The fix? Replace aging belts and hoses as part of your PM schedule, not after they’ve shredded or ruptured. This is one of the easiest and cheapest truck repairs to do early, and one of the most painful if ignored.
7. HVAC System Neglect is a Driver Retention Killer
You might not think of the AC or bunk heater as critical truck components. But ask any long-haul driver stuck in 90-degree weather or freezing temps with a dead blower motor, and comfort matters.
Ignoring HVAC repairs might save money this week, but it could cost you a good driver next month. Driver turnover already bleeds cash. Keeping cabs comfortable is a low-cost way to show you care and keep them loyal.
8. DEF and Emissions System is The Compliance Trap
Today’s emissions systems are complex and expensive when they go down. A clogged DPF, faulty NOx sensor, or malfunctioning EGR valve won’t just kill power; it’ll trigger derate mode or force shutdowns.
Many operators delay DEF-related truck repairs because of cost or downtime. But that delay can turn into missed loads and expensive regeneration services. If you’re running newer trucks, keeping emissions systems healthy is non-negotiable.
9. Loose Suspension Components are The Silent Ride Destroyers
When your driver is grumbling that he can hear some strange noises or enjoys bouncy rides, do not jump to conclude that it is a bad road. Worn or Loose suspension components, e.g., bushings, torque rods, or shocks, may wear tires out of round, break axles, and knock the car out of alignment.
Ignoring such components translates to extra cash on tires, handling problems, and accidents that are likely to occur. Early detection of these problems during the repair of trucks will help to avoid a series of mechanical failures.
10. Transmission and Clutch Slippage take you to The Expensive Stall
Not every fleet has the luxury of a spare tractor. If a truck goes down with a cooked clutch or transmission issue, that’s revenue gone until you’re back on the road. Drivers may “ride” a slipping clutch for weeks without saying anything.
Problems can be identified in the early stages by carrying out regular checks on transmission and feedback supplied by drivers. Teaching drivers to notice when they are slipping or gear-grinding can have you ahead of the game in maintenance before a $5000 repair becomes a $12000 replacement.
Stop Waiting for Something to Break
We understand; you have limited time, limited funds, and limited time to include yet one more visit to the shop. Yet remaining a step ahead of such afterthought concerns means you have moving trucks, timely deliveries, and secure drivers.
This is why putting money in routine truck repairing is not an expenditure; it is a plan. Whether you are a mobile mechanic or coming in person to the shop, the accurate repair partner not only repairs what is wrong, but he or she will assist you in seeing what is soon to break.
You need not wait until a DOT inspection or a roadside breakdown to get reminded of what is being overlooked. Have a fleet in the best conditions, customers satisfied, and your wallet full. The brainy move? Put truck repair on your monthly game plan, not a play day scrimmage.